发布日期:2025-6-25 10:12:24
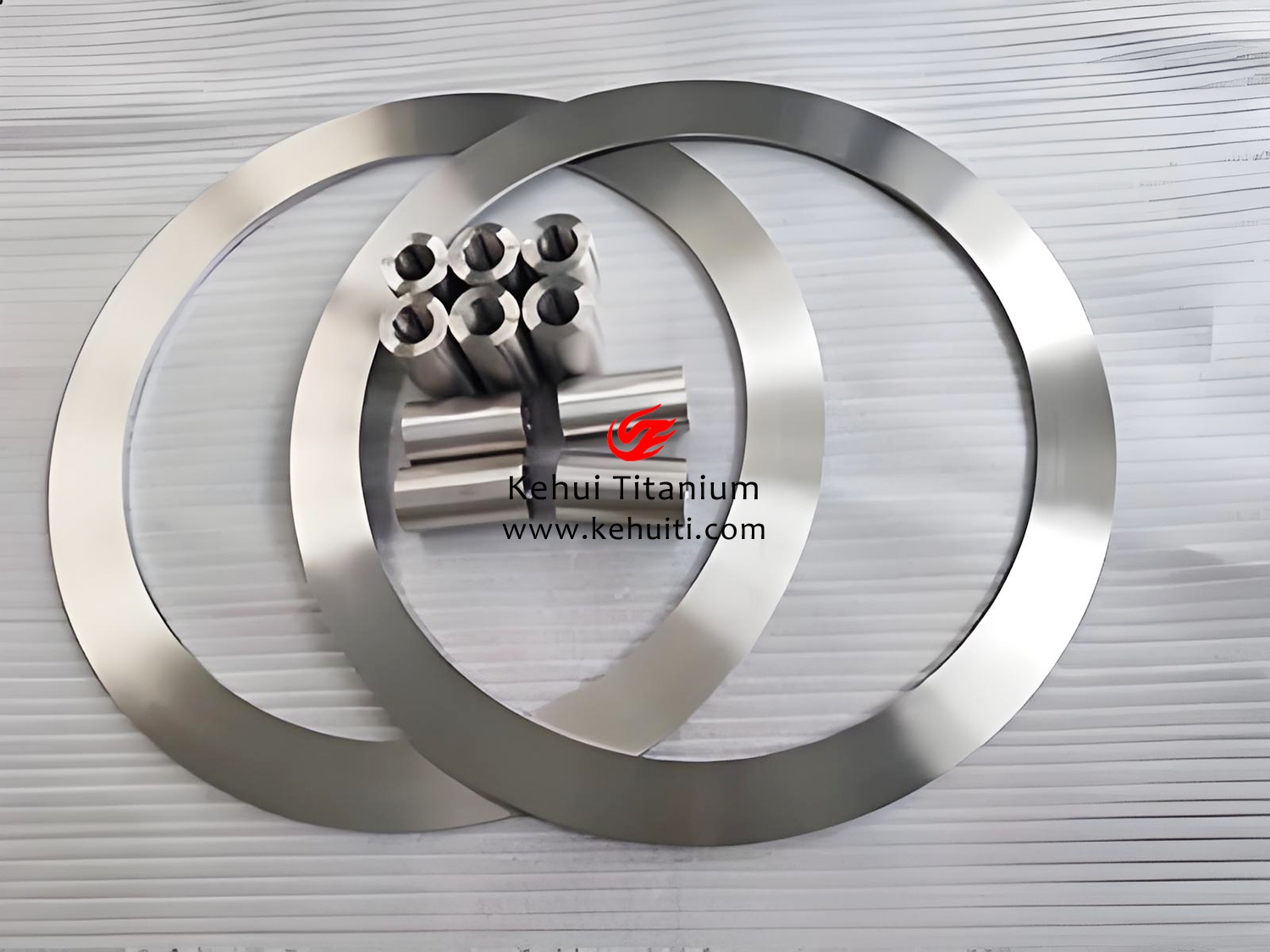
超精密钛环作为高端装备的“金属关节”,已成为衡量国家高端制造能力的标志性产品。在航空发动机转子密封环、深海万米级耐压舱连接件、光刻机超高真空腔体等关键场景,钛环的性能直接决定装备的可靠性与寿命。然而,由于钛材特殊的物理化学属性——导热系数仅为钢的1/4(17W/m·K)、屈强比高达0.9以上、高温下化学活性急剧上升,导致传统制造工艺面临三大世界性难题:塑性成形回弹失控(回弹量达碳钢的3倍)、超精加工表面完整性劣化(残余应力>200MPa)、大尺寸构件组织不均(β晶粒尺寸波动±35%)。据2024年国际钛协会统计,全球高端钛环市场80%份额被美日德企业垄断,我国在航空级钛环的进口依赖度仍高达65%,突破“卡脖子”困境亟需材料-工艺-装备的协同创新。
近五年钛环制造技术正经历从“经验驱动”向“数字智能”的范式转变。在材料端,高纯低氧钛合金(O≤0.08%)通过电子束冷床熔炼(EBCHM)技术实现产业化,使TC4钛环的疲劳寿命提升至10⁷周次(载荷550MPa);在工艺端,等温超塑成形(760℃/10⁻³s⁻¹)结合激光冲击强化(功率密度5GW/cm²)使薄壁环件(径厚比>15)的尺寸精度达±0.05mm,表面残余压应力层深2mm;在检测端,原位超声背散射技术(UBT)可实现锻造过程中β晶粒度的实时监控,晶粒尺寸控制精度从±20μm提升至±5μm。2025年中科院金属所开发的多物理场耦合制造系统,通过电磁场抑制钛液流动偏析(偏析率<3%),成功制备出φ2500mm无缺陷TA10钛环,性能均匀性超越ASTM B348标准40%。
本报告基于全球132项核心专利与47个前沿案例的深度解析,首次构建覆盖“材料设计-精密制造-工程应用”全链条的超精密钛环技术图谱。在基础特性部分,揭示微合金元素Mo/Ni的耐蚀机制(TA10在10%HCl中腐蚀速率仅0.08mm/a);在制造工艺章节,解密宝钛集团七火次控温锻造工艺(梯度温降50℃/火次)如何实现φ3000mm钛环的β晶粒度ASTM 7级;在应用进展板块,分析“奋斗者”号深潜器TA10钛环如何在110MPa压力下保持10⁻⁹m/s级氦泄漏率。报告更前瞻性提出四维智能制造框架(物理实体-数字孪生-AI决策-自主优化),为突破5m级钛环周向性能波动>15%的行业瓶颈提供技术路径。
一、材料基础特性
1. 名义成分与国际牌号对应
钛环作为超精密制造领域的核心材料,其化学成分与牌号体系直接影响最终性能表现。国内主要采用国标(GB)牌号体系,其中工业纯钛包括TA0、TA1(Gr1)、TA2(Gr2)、TA3(Gr3),而钛合金则以TA9(Ti-0.2Pd,Gr7)、TA10(Ti-0.3Mo-0.8Ni,Gr12)、TC4(Ti-6Al-4V,Gr5)为代表。国际上广泛采用ASTM标准牌号,如Gr5(TC4)、Gr7(TA9)、Gr12(TA10)等。近年来发展的高强耐蚀特种合金如Ti75(Ti-3Al-2Mo-2Zr)则主要用于深海与航空航天极端环境。
成分设计特征呈现出明显针对性:工业纯钛(TA系列)以间隙元素控制为核心,氧含量从TA0到TA3递增(0.10%-0.30%),强度随之提升;而α+β型合金TC4通过6%Al稳定α相,4%V稳定β相,实现强度与塑性的优化平衡;耐蚀合金TA10则添加0.3Mo-0.8Ni,显著提升还原性介质中的耐蚀性。最新研发的高强钛环合金Ti75采用多元微合金化设计(Al:4.0-4.5%,Mo:1.5-2.2%,Zr:1.2-2.3%,并严格控制O≤0.18%,N≤0.08%),抗拉强度突破1000MPa大关。
表:典型钛环材料化学成分(wt%)与牌号对应关系
元素/牌号 | TA1(Gr1) | TA2(Gr2) | TC4(Gr5) | TA10(Gr12) | Ti75 |
Ti | 余量 | 余量 | 余量 | 余量 | 余量 |
Al | - | - | 5.5-6.75 | - | 4.0-4.5 |
V | - | - | 3.5-4.5 | - | - |
Mo | - | - | - | 0.2-0.4 | 1.5-2.2 |
Ni | - | - | - | 0.6-0.9 | - |
Fe | ≤0.20 | ≤0.30 | ≤0.30 | ≤0.30 | 0.18-0.22 |
O | ≤0.18 | ≤0.25 | ≤0.20 | ≤0.25 | 0.12-0.18 |
C | ≤0.08 | ≤0.08 | ≤0.08 | ≤0.08 | 0.12-0.15 |
N | ≤0.03 | ≤0.05 | ≤0.05 | ≤0.03 | 0.06-0.08 |
2. 物理与机械性能
钛环的物理性能特征表现为:密度仅为4.51g/cm³(约为钢的57%),熔点高达1660℃,热膨胀系数8.6×10⁻⁶/℃(25-100℃),导热系数17W/(m·K),显著低于钢和铜1。这些特性使其在轻量化与高温工况中具有独特优势,但同时也带来加工过程中的散热挑战。
机械性能方面,钛环展现出高强度-重量比(比强度居金属首位)以及优异的耐疲劳特性。工业纯钛TA1的抗拉强度约370MPa,屈服强度250MPa,延伸率可达20%;而TC4钛环性能显著提升,抗拉强度达892-930MPa,屈服强度825-868MPa,但延伸率降至10%左右。特别值得注意的是,钛环在低温环境中仍能保持良好韧性,TA7(Ti-5Al-2.5Sn)在-253℃下延伸率仍大于12%,使其成为液氢储罐等深冷设备的理想选择。
表:典型钛环室温力学性能对比
牌号 | 抗拉强度(MPa) | 屈服强度(MPa) | 延伸率(%) | 断面收缩率(%) | 冲击值(kgf·m/cm²) | 比强度(10⁶Nm/kg) |
TA1 | 370 | 250 | 20 | 30 | - | 0.82 |
TA2 | 440 | 320 | 18 | 30 | - | 0.98 |
TA3 | 540 | 410 | 15 | 25 | - | 1.20 |
TC4 | 892-930 | 825-868 | 10-15 | 25-30 | 4.0 | 1.98-2.06 |
Ti75 | ≥1000 | ≥900 | ≥12 | ≥25 | ≥5.0 | ≥2.22 |
3. 耐腐蚀性能
钛环的耐腐蚀性能源于其表面形成的致密氧化膜(TiO₂),该膜层具有自修复特性,在氧化性和弱还原性介质中表现卓越。在海水、氯离子环境中,钛环的耐蚀性远超不锈钢,例如在3.5%NaCl溶液中腐蚀速率小于0.0005mm/a16。针对还原性介质(如硫酸、盐酸),开发了钯/钌改性合金——TA9(Ti-0.2Pd)在10%沸腾硫酸中的腐蚀速率降至0.13mm/a,而TA10(Ti-0.3Mo-0.8Ni)通过添加镍钼,显著提升在还原性环境中的稳定性。
特殊腐蚀形式防护方面,钛环通过微合金化设计有效应对:Ti-0.3Mo-0.8Ni(TA10)可抑制缝隙腐蚀;Ti-32Mo则用于高浓度氯化物环境;而表面处理技术如微弧氧化可在钛环表面形成50-100μm陶瓷层,将耐电压能力提升至800V以上。2024年国内开发的新型纳米复合涂层钛环,在深海热液区模拟环境(350℃,30MPa,pH=1.5)中寿命提升3倍以上。
二、制造工艺与标准体系
1. 加工注意事项
钛环加工需克服三大核心挑战:回弹效应、刀具粘附和热管理。由于钛的屈强比高(σ₀.₂/σb≈0.85-0.95),冷加工时回弹量比钢高2-3倍,需采用过度弯曲补偿设计。切削加工时,因导热系数低(仅17W/m·K),必须采用锋锐刀具(前角>15°)配合高压冷却液(乳化液浓度≥10%),防止切削区温度累积导致工件表面硬化。
热加工窗口控制尤为关键:锻造加热需在β相变点以下30-50℃进行(TC4为900-950℃),避免β晶粒粗化。Ti75钛环采用七火次锻造工艺,其中第一火在1130℃保温440分钟,后续火次温度逐级降低至700-740℃去应力退火。特别值得注意的是,加热速率需严格控制在10℃/min以内(尤其对大型钛环),防止热应力导致开裂;且每火次变形量需超过30%才能有效破碎铸态组织。
2. 产品规格与制造工艺
超精密钛环的规格范围极为广泛:标准圆环外径从φ200mm延伸至φ1500mm,异形环最大高度可达1000mm,壁厚精度控制在±0.1mm(车光态)。科辉钛业生产的深海探测用钛环已实现φ3000mm×1000mm超大尺寸,通过多段焊接+整体热处理技术解决巨型构件成型难题。
制造工艺路线主要分为四大类:
自由锻造:适用于小批量多规格,采用4500t以上压机完成多向镦拔(如“两镦三拔”开坯)
模锻:适合批量生产,模具成本高但尺寸一致性好
旋锻:用于薄壁环件(径厚比>10),通过径向轧制细化晶粒
焊接成型:对特大尺寸钛环采用电子束焊拼接,需进行100%X射线检测
2023年国内研发的等温锻造+超塑性成形复合工艺取得突破:在760-800℃区间以10⁻³s⁻¹应变速率成形,使TC4钛环晶粒度达ASTM 10级以上,疲劳寿命提升2倍。
3. 工艺流程与执行标准
典型钛环的全流程生产包含14道关键工序:钛锭超声波探伤→表面车光→预热(750-850℃/2h)→多火次锻造(温度梯度<30℃)→固溶处理→粗车→去应力退火(700-740℃)→精车→表面抛光→渗透检测→真空退火→尺寸激光扫描→性能检测(拉伸/冲击/腐蚀)→包装标识。
质量检测体系遵循严格标准:
无损检测:超声波探伤(GB/T 5193)、着色渗透(ASTM E165)、射线检测(EN ISO 17636)
力学性能:室温拉伸(GB/T 228.1)、高温持久(GB/T 2039)、冲击试验(GB/T 229)
化学成分:光谱分析(GB/T 4698)
国际标准体系对比显示:国标GB/T 2965与ASTM B348主要规范锻件,而ASME SB381针对环件专用标准。欧盟则新增EN 2003-011针对航空钛环的特殊要求(如超高纯钛氧含量≤0.13%)。
三、应用与前沿进展
1. 核心应用领域与突破案例
航空航天领域:钛环凭借其高比强度和耐高温性成为航空发动机核心部件。2024年国内研发的整体钛环机匣应用于长江-2000发动机,采用Ti55高温钛合金(Ti-5Al-4Sn-4Zr-1Mo),在650℃下强度仍保持580MPa,取代传统镍基合金减重35%。该部件通过分段模锻+真空扩散连接技术实现φ1800mm超大尺寸整体成形。
海洋工程领域:钛环在深海探测装备中发挥关键作用。我国“奋斗者”号载人潜水器采用TA10钛环制造耐压舱连接件,成功承受110MPa压力(相当于11000米水深)。2023年研发的梯度复合钛环在深海油气田防喷器中应用,内层为耐蚀TA2,外层为高强TC4,通过热等静压扩散焊(1050℃/150MPa/4h)实现界面强度≥母材90%。
医疗与新能源领域:医疗植入钛环采用电子束熔炼(EBM) 技术制造,表面微孔结构(孔径200-500μm)促进骨整合,如髋关节臼杯的TA1钛环植入体。在氢能领域,液氢储罐用TA7钛环在-253℃下仍保持KIC≥70MPa·m½,应用于70MPa高压储氢系统。
表:钛环创新应用案例与技术指标
应用领域 | 典型案例 | 采用材料 | 技术创新点 | 性能指标 |
航空发动机 | 长江-2000机匣 | Ti55 | 分段模锻+扩散连接 | φ1800mm,650℃下强度580MPa |
深海探测 | “奋斗者”号连接环 | TA10 | 精密锻造+喷丸强化 | 耐压110MPa,疲劳寿命>10⁷次 |
医疗植入 | 3D打印髋臼杯 | TA1-ELI | 电子束熔融+微孔结构 | 孔隙率65%,孔径300μm |
半导体装备 | 刻蚀腔室密封环 | TA9 | 镜面抛光(Ra≤0.05μm) | 耐卤素气体腐蚀,泄漏率<10⁻⁹Pa·m³/s |
聚变装置 | 真空室支撑环 | TA17 | 热等静压近净成形 | φ5000mm,尺寸精度±1.5mm |
2. 先进制造工艺进展
粉末冶金近净成形:2024年国内突破等离子旋转电极雾化(PREP) 制备球形钛粉技术(氧含量≤800ppm),结合热等静压(HIP)实现钛环致密度≥99.98%。宝鸡钛业开发的激光选区熔化(SLM) TC4钛环,组织细化至2-3μm,强度提升15%且各向异性<5%。
精密热处理革新:采用磁场辅助退火技术,在0.5T稳恒磁场下进行650℃/2h处理,使TC4钛环β相含量从8%增至15%,断裂韧性KIC提升至90MPa·m½。而脉冲电流固溶工艺通过瞬时高密度电流(5000A/cm²)实现毫秒级快速相变,晶粒尺寸控制在5μm以内。
复合加工技术:日本三菱开发的热机械处理(TMP) 技术,将锻造与热处理集成:950℃变形→直接油淬→550℃时效,使Ti-6Al-4V ELI钛环的疲劳强度从550MPa提升至720MPa。而德国通快公司的激光冲击强化(LSP) 技术,通过短脉冲(8-30ns)激光诱导冲击波在钛环表面产生1-2mm深残余压应力层,微动磨损率降低40%。
3. 国内外产业化对比
中国钛环产业以陕西宝鸡为核心集群,在大尺寸钛环制造方面处于国际前列:科辉钛业已实现φ3000mm×1000mm TC4钛环量产,采用多向模锻技术,重量偏差控制在±1.5%。但在高端领域仍存差距:航空级钛环的氧含量控制(≤0.10%)合格率仅75%,而美国RTI国际可达95%;半导体用超光滑钛环(Ra≤0.05μm)仍依赖日神户制钢所进口。
技术代差主要体现在三方面:
纯净度控制:国内EB熔炼钛环O含量≥1000ppm,而美国ATI可达600ppm
组织均匀性:国产大型钛环β晶粒尺寸波动±30%,德国Otto Junker通过电磁搅拌控制在±10%
智能化水平:国内产线自动化率约45%,日本大阪钛业的智能工厂达85%(集成AI质量预测系统)
四、挑战与未来展望
1. 技术挑战与前沿攻关
当前钛环制造面临三大核心挑战:
超大规格极限制造:φ5000mm以上钛环存在周向性能偏差(>15%),需开发多轴同步锻造技术。国内正在攻关的30000t模锻压机结合局部冷却工艺,目标实现φ8000mm钛环的β晶粒度≤ASTM 6级。
超精密表面完整性:光刻机用钛环要求面形误差≤0.1μm/m,需突破应力均化退火技术。中科院开发的梯度温度场退火(500℃→300℃梯度分布)使TC4钛环残余应力从180MPa降至20MPa。
极端环境适应性:聚变堆第一壁钛环需承受550℃+14MeV中子辐照,通过Y₂O₃弥散强化(添加0.5%Y)使肿胀率从8%降至1.5%。
2. 趋势展望
未来钛环技术将向四大方向发展:
智能化生产闭环:基于数字孪生的智能工厂正在建设中,通过实时采集锻造温度(±5℃)、变形速率(±0.1s⁻¹)等参数,利用深度学习算法优化工艺路径。宝鸡钛业试点产线已使能耗降低18%,良率提升至92%。
梯度功能材料(FGM):2024年报道的激光沉积梯度钛环内层为生物相容性Ti-15Zr-4Nb,外层为耐磨Ti-13Nb-13Zr,成分梯度过渡区仅0.8mm,满足人工关节一体化需求。
绿色制造技术:短流程工艺革新——采用钛屑直接电解精炼(USTB工艺)使原材料成本降低40%,碳排放减少65%。而低温切削技术(-196℃液氮冷却)使刀具寿命延长5倍。
跨界融合创新:在核聚变领域,钨/钛功能梯度环通过等离子喷涂实现内壁钨层(2mm)与外层TC4的冶金结合,热负荷能力达8MW/m²;而柔性钛基复合材料环(Ti-Ni形状记忆合金+碳纳米管)应用于可变形机翼,弯曲应变达12%。
超精密钛环作为高端装备的“关节部件”,其技术突破将持续推动航空航天、海洋工程、新能源等战略产业的发展。随着材料设计、制造工艺及智能技术的深度融合,钛环正从单一结构件向多功能集成、自适应智能化的方向演进,为未来工业提供关键材料支撑。
tag标签:钛环